100%-Planung bringt Qualitätsgewinn im Schaltschrankbau
Die a-on AG in Neufahrn bei München hat einen durchgängigen Prozess für die Planung und den Bau von Schaltschränken realisiert und nutzt dabei die EPLAN Plattform.
Von der Kalkulation über die Elektroplanung bis hin zur mechanischen Bearbeitung und zur Aderkonfektionierung: Die a-on AG in Neufahrn bei München hat einen durchgängigen Prozess für die Planung und den Bau von Schaltschränken realisiert und nutzt dabei die EPLAN Plattform. Eigentlich wollte man auf diese Weise vor allem die Qualität im Konstruktionsprozess optimieren – jetzt profitiert man auch von rund 30% Zeitersparnis in der Fertigung. Das 2002 gegründete Unternehmen arbeitet für namhafte internationale Unternehmen im Anlagen- und Sondermaschinenbau aus ganz verschiedenen Branchen. Das Spektrum reicht hier von der Lebensmittelproduktion über Holzverarbeitung, Kunststofftechnik und Automotive bis zur Pharmaindustrie. Eines ist aber den Schaltschränken, die in Neufahrn geplant und gebaut werden, gemein. Josef Altmann, Vorstand der a-on AG: „Jedes Produkt ist ein Unikat.“ Dabei deckt das Unternehmen ein breites Engineering-Portfolio ab: a-on übernimmt nicht nur die Hardware- und Softwareplanung der Steuerungstechnik, sondern sehr häufig auch die Planung der Leit- und Visualisierungssysteme sowie die Elektromontage- und Inbetriebnahme der Anlage vor Ort. Ziel: Durchgängige Prozesse
a-on arbeitete von Beginn an mit EPLAN und hat sehr frühzeitig mit der Migration auf die neue Plattform begonnen. Projektleiter Dipl.-Ing (FH) Lorenz Huber: „Die Umstellung fällt nicht schwer, weil zahlreiche Automatismen dabei helfen. Zudem verbessern sich die Prozesse durch die EPLAN Plattform: Als sehr sinnvoll empfinden wir das geräteorientierte Arbeiten.“ Die Umstellung erfolgte auch deshalb sehr früh, weil a-on großen Wert auf durchgängige Prozesse legt. Josef Altmann: „Wir sehen das als ein zentrales Kriterium, mit dem wir uns im Wettbewerb unterscheiden. Die Durchgängigkeit ist aus unserer Sicht die Voraussetzung für hohe Qualität und Standardisierung in der Konstruktion.“ Verbindung von E-CAD und PPS schon in der Kalkulation
Das Arbeiten auf der EPLAN Plattform beginnt deshalb schon mit der Kalkulation. Hier nutzt a-on die Software „PMS“ als Kopplung des E-CAD-Systems zur Produktionsplanung und –steuerung (PPS). Josef Altmann: „Unser gesamtes operatives Geschäft stützt sich auf E-CAD und PPS. Deshalb kommt der Verbindung beider Systeme so große Bedeutung zu.“ In der Kalkulation bietet der wechselseitige Austausch von CAD und PPS den Vorteil, dass der Vertrieb in Kooperation mit der Elektrokonstruktion sehr genau die Kosten eines Projektes kalkulieren kann. Dabei verwendet man Basisbaugruppen, die in EPLAN hinterlegt sind. Das erfordert vielleicht einen höheren administrativen Aufwand, der sich jedoch rechnet. Die Kalkulation ist sehr exakt und man hat schon eine gute Datenbasis für die Konstruktion, wenn der Auftrag erteilt wird. Die Stückliste eines Projektes beispielsweise steht beiden Systemen zur Verfügung, so dass Material und Massen stets transparent sind, und dank der Verbindung von EPLAN zu PMS kann der Konstrukteur per Knopfdruck eine Bestellung auslösen. Diese Durchgängigkeit, die bei der Kalkulation beginnt, endet erst beim Abschluss des Projektes, mit der Fakturierung. Daten aus dem PPS-System und dem EPLAN Data Portal
Auch innerhalb der Elektrokonstruktion hat a-on konsequent einen durchgängigen Informationsfluss etabliert. Dabei hat man darauf geachtet, die von EPLAN Electric P8 gebotenen Möglichkeiten der Standardisierung zu nutzen. So erleichtert eine umfassende Bibliothek von Komponenten den Konstrukteuren die Arbeit. Lorenz Huber: „Wir haben rund 25.000 Artikel mit Artikelnummer und Zeichnungen im System gespeichert. Viele haben wir aus dem Produktions-Planungs-System übernommen. Von anderen Komponenten haben wir bei den Herstellern Daten und Zeichnungen angefordert oder heruntergeladen und in einheitliche Formate gebracht. Und seit das EPLAN Data Portal online ist, laden wir dort viele Daten herunter.“ Dass es keine Kleinigkeit ist, 25.000 Artikel in eine einheitliche Datenbasis zu überführen, bestreitet man bei a-on nicht. Aber alle Beteiligten sind davon überzeugt, dass sich der Aufwand lohnt: Er führt zu einer Standardisierung und einer Verwendung von Gleichteilen, die letztlich die Qualität der Konstruktion erhöhen. Josef Altmann: „Wir haben auch vor der Migration auf die neue Plattform schon selbst erstellte Automatisierungs-Tools genutzt, um einen hohen Qualitätsstandard zu erreichen und die Effizienz der Prozesse zu verbessern. Mit der einheitlichen Datenplattform haben wir nun ganz andere Möglichkeiten der Automatisierung.“ 3D-Layout mit EPLAN Cabinet
Die in EPLAN Electric P8 generierten Daten werden in EPLAN Cabinet weiterverarbeitet. Das System übernimmt die elektrotechnischen Projektdaten. Auf deren Basis wird ein professionelles, dreidimensionales Schaltschrank-Layout erstellt, das die Bauteile optimal platziert und auch die Kabellängen sowie die nötigen Ausschnitte und Bohrungen im Schaltschrank ermittelt. Selbstverständlich berücksichtigt EPLAN Cabinet dabei die individuellen Einbaubedingungen wie Mindestabstände und Klimatisierung. Für das Rittal-Schaltschrankprogramm, kann man die Daten der Schaltschränke direkt aus dem RiCAD 3D-Produktkatalog übernehmen. Direkte Verbindung zur Fertigung
Soweit befindet man sich noch auf der Ebene der Konstruktion. Aber auch die Fertigung ist in den Informationsfluss integriert. So werden die CNC-Daten zur individuellen Fertigung des Schaltschrankes direkt aus EPLAN Cabinet heraus an eine CNC-Anlage von Steinhauer übermittelt. Und die Aderkonfektionierung erfolgt auch weitestgehend automatisiert auf der Basis der EPLAN Cabinet-Routing-Daten. Lorenz Huber: „Diese Automatisierung ist sehr komfortabel. Die Längen der Drähte sowie deren Anfangs- und Endbezeichnung sind definiert, auch die Betriebsmittelkennzeichnung wird automatisch generiert. Ebenso lässt sich eine Einzeladerbeschriftung, die bei Anlagen nach UL bereits Standard ist, leicht realisieren. Und weil die Routing-Daten festgelegt sind, entsteht quasi automatisch ein einheitlicher Standard für die Platzierung und Montage der Bauteile.“ Der schnelle Weg zum Schaltschrank
EPLAN Cabinet schafft ideale Voraussetzungen für eine Parallelisierung der Arbeit: „Aufgrund der Einzeladerkonfektionierung, kann die Fertigung quasi schon mit der Verdrahtung beginnen, bevor die Komponenten montiert sind. Wir können also den Start der Produktion vorverlegen und zusätzlich die Lieferzeit verkürzen.“ Zur Verkürzung der Produktionszeit trägt auch bei, dass a-on die Klemmen und Hutschienen in EPLAN Electric P8 konstruiert und zum Teil bei den Lieferanten einbaufertig konfektionierte Module bestellt. All diese Automatismen schaffen die Voraussetzung dafür, dass die Montage des Schaltschranks schnell und fehlerfrei erledigt wird. Lorenz Huber: „Wir verdrahten nach Liste, nicht nach Schaltplan. Der Stromlaufplan wird nur zur 100%-Funktionsprüfung nach der Montage genutzt.“ Fazit: Konstruktion aufgewertet
Nach der Migration auf die EPLAN Plattform sind die Verantwortlichen von a-on rundum zufrieden mit dem Ergebnis. Josef Altmann: „Zuvor haben wir vielleicht 80% des Schaltschrankes geplant, nun sind es 100%. Das war unser Ziel.“ Damit einher ging auch eine Aufwertung der Konstruktion: Sie muss genauer arbeiten und – unterstützt von den automatisierten Prozessen – mehr Festlegungen treffen. Die Montage hat demnach weniger Spielraum, aber genau das ist gewünscht, denn auf diese Weise steigt die Qualität. 100% Planung führt zu 30% Zeitersparnis
Sehr positiv wird auch die neue Grundlage der Konstruktion bewertet: Die Datenbank und die Objektorientierung schaffen die Voraussetzung für die durchgängigen, standardisierten Prozesse, die für a-on im Zentrum der neuen Konstruktionsprozesse stehen. Dabei hat man auch noch einen zusätzlichen Vorteil erzielt, der anfangs gar nicht im Fokus stand. Josef Altmann: „Wir sind davon ausgegangen, dass der Zeitaufwand für die neue Methodik der gleiche ist und der Qualitätsgewinn den Unterschied ausmacht. Nun stellen wir aber fest, dass wir rund 30% schneller fertigen. Wir profitieren also von höherer Qualität und einem deutlichen Zeitgewinn. Damit haben wir die Zeit der Krise gut genutzt, um besser und effizienter zu werden: Mit diesem Vorsprung können wir uns noch besser als zuvor im Wettbewerb unterscheiden.“
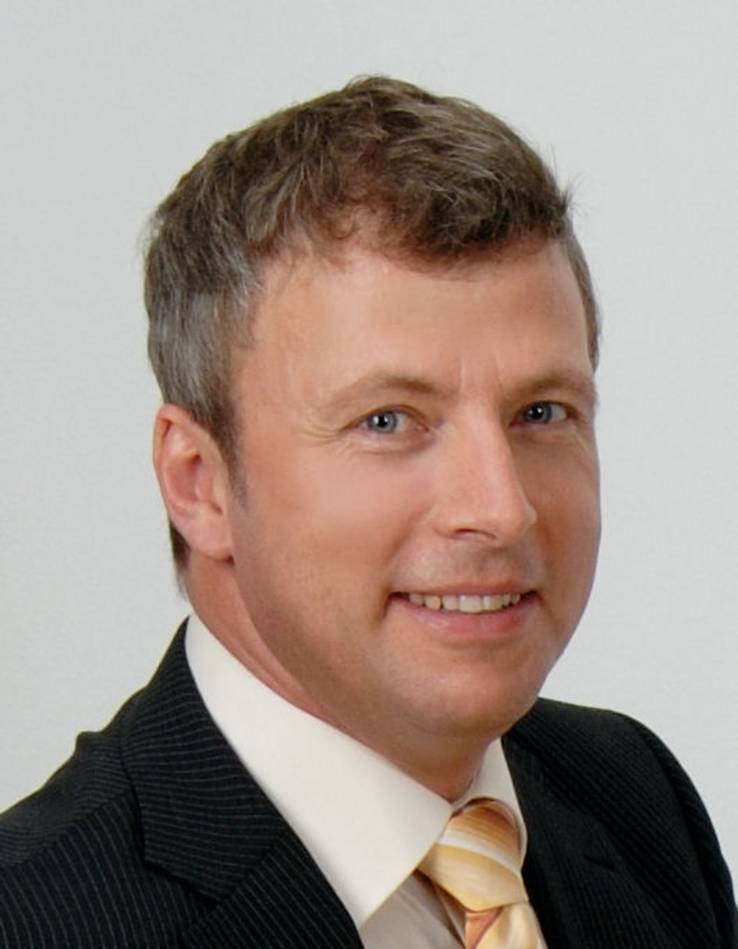
„Mit der durchgängigen EPLAN Plattform haben wir nun ganz andere Möglichkeiten der Automatisierung“, so Josef Altmann, Vorstand der a-on AG.
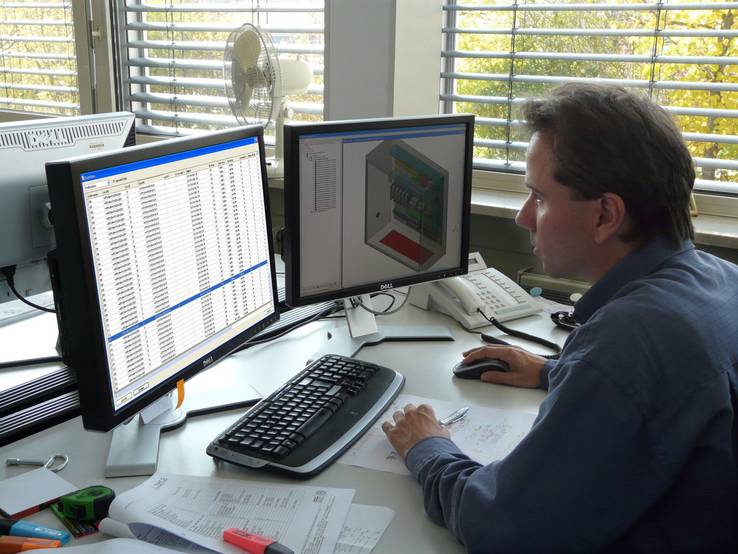
Projektleiter Dipl.-Ing (FH) Lorenz Huber profitiert von zahlreichen Automatismen bei der Projektierung. „Die Prozesse durch den Einsatz der EPLAN-Plattform verbessern sich - als sehr sinnvoll empfinden wir das geräteorientierte Arbeiten.“
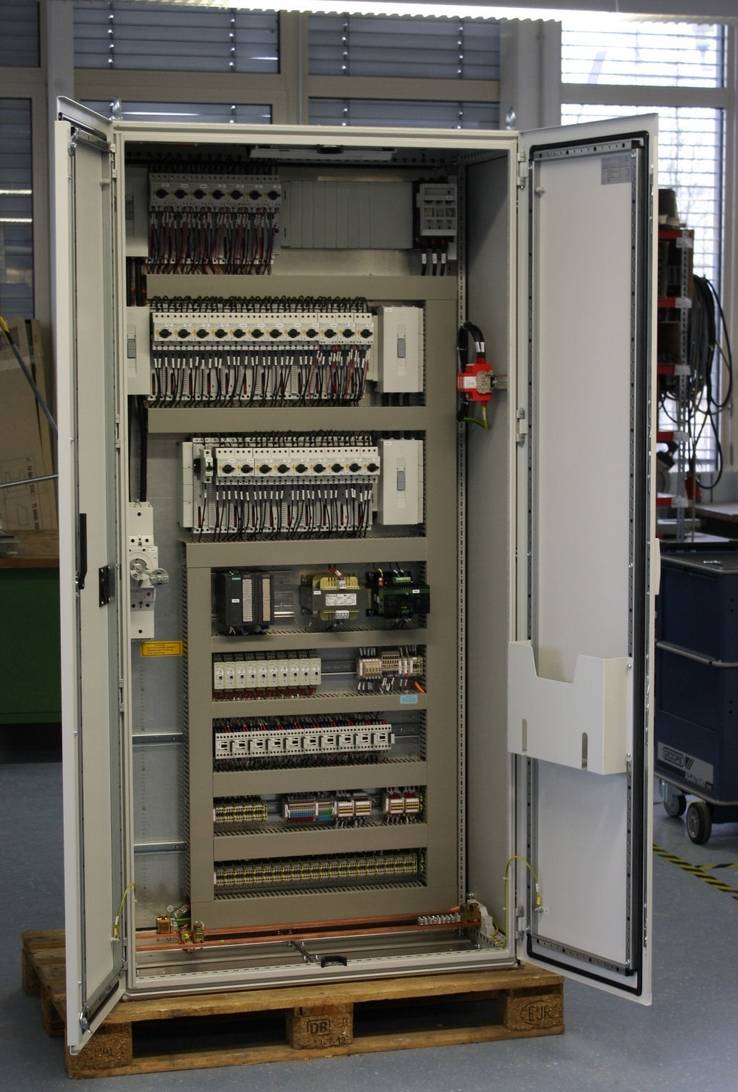
Die a-on AG deckt ein breites Engineering-Portfolio ab: Hard- ware- und Softwareplanung der Steuerungstechnik wie auch die Planung der Leit- und Visualisierungssysteme, Elektro- montage- und Inbetriebnahme vor Ort.