Konstanter, standardisierter Wandel
Das einzig Beständige ist der Wandel
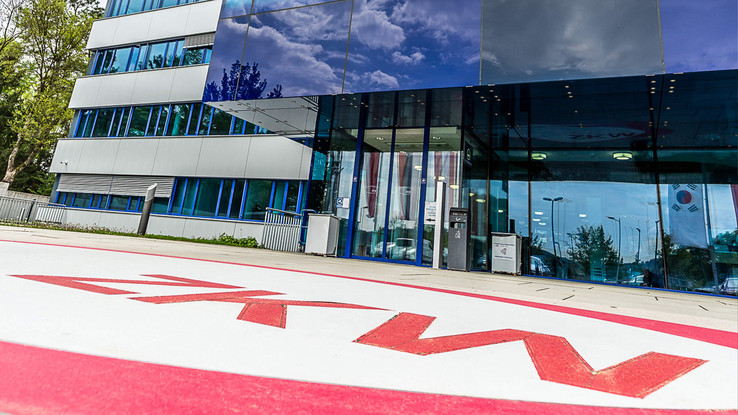
Premium-Lichtsysteme für die weltweite Automobilindustrie: die ZKW Group in Wieselburg (Niederösterreich).
© www.martingold.at
Das einzig Beständige ist der Wandel – so könnte man die Produktion von ZKW wohl am Besten beschreiben. Und dieser Wandel stellt hohe Herausforderungen an das Engineering, sind doch die modular aufgebauten Montagelinien in einem andauernden Prozess immer wieder an neue Produkte anzupassen. Um diese hohe Flexibilität im Engineering zu erreichen, setzt ZKW seit kurzem auf EPLAN.
Die ZKW Group mit Headquarter in Wieselburg (Niederösterreich) entwickelt und produziert Premium-Lichtsysteme samt Elektronik für die weltweite Automobilindustrie. ZKW kann auf ein Netzwerk an über den Globus verteilten Produktionsstandorten zurückgreifen und so die hohen Anforderungen der Kunden an die Qualität und Liefertreue perfekt erfüllen. Das Kompetenzzentrum für Forschung und Entwicklung befindet sich am Standort in Wieselburg, wo in Summe rund 3.000 Mitarbeiter tätig sind (weltweit sind es etwa 10.000). Entwickelt und erzeugt werden Lichtsysteme. Doch was sich oberflächlich betrachtet einfach nach Schweinwerfern und Rückleuchten für Pkw und Lkw anhört, entpuppt sich bei näherer Betrachtung als höchst anspruchsvolles technologisches System. Dahinter verbirgt sich etwa eine 360-Grad-Beleuchtung für ein Auto, deren Sensorik bzw. Aktorik im Zuge des autonomen Fahrens eine gänzlich neue, wesentliche Bedeutung beikommt. Insbesondere in dieses Zukunftsthema steckt ZKW eine ganze Menge an Forschungsenergie und ist daher ständig auf der Suche nach Entwicklungsingenieuren. Ein gutes Beispiel für eine dieser Innovationen sind die neuartigen „DLP®“-LED-Scheinwerfer, der aktuell in den Range Rover eingebaut werden. Diese erzeugen nicht nur stufenloses, blendfreies Fernlicht, das entgegenkommende oder andere Verkehrsteilnehmer automatisch ausblendet. Die smarte, digitale Frontbeleuchtung ermöglicht es auch, animierte Bilder auf die Straße zu projizieren.
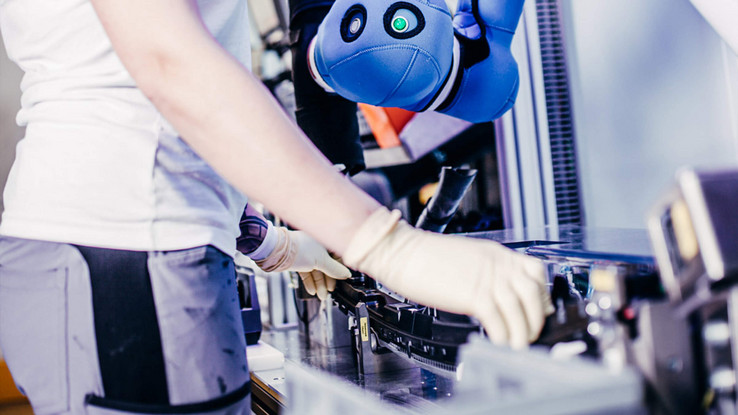
COBOTs, also kollaborierende Roboter, arbeiten gemeinsam mit den Montagemitarbeitern am Fertigungsband.
© ZKW
Anpassen, umbauen, adaptieren
Selbstverständlich stellen diese und ähnliche innovative Technologien höchste Anforderungen an die Produktion von ZKW, sind doch zum Beispiel sensible Kameras, Ultraschallsensoren oder Radargeräte in die Scheinwerfer zu integrieren. „Zudem testen wir diese Systeme und Technologien vor Auslieferung zu 100 Prozent. Das stellt hohe Ansprüche an unsere hauseigene Prüftechnik“, erklärt Ing. Alexander Klemenz, Team Leader Process Engineering Operation Resources/Control Engineering bei ZKW. So zeigt sich: Das Unternehmen agiert in einem innovationsgetriebenen Markt, in dem nur die Besten bestehen. Damit das auch in Zukunft so bleibt, investiert der Konzern viel Energie in seine Montagelinien. Und von diesen gibt es in Wieselburg Dutzende: Eine exakte Zahl lässt sich kaum nennen, da auf Grund der enorm hohen Anzahl unterschiedlicher Lichtsysteme sämtliche Montagelinien einer laufenden Anpassung unterworfen sind. Dafür unterhält ZKW einen eigenen Anlagenbau, der die Montagelinien und Prüftechnologien selbst entwickelt, errichtet, adaptiert und serviciert. Übrigens: ZWK setzt seit 2019 auf sogenannte COBOTs, also kollaborierende Roboter, die gemeinsam mit den Montagemitarbeitern am Fertigungsband arbeiten. Alexander Klemenz fasst zusammen: „Wir müssen unsere komplexen, präzisen Montagelinien laufend an andere bzw. neue Produkte und Technologien anpassen, was mit einem hohen Engineering-Aufwand verbunden ist. Diesen möchten wir aber natürlich so klein wie möglich halten.“
Konstruieren, standardisieren, automatisieren
Da diese Anforderungen mit dem bisher eingesetzten Engineering-Tool kaum mehr zufriedenstellend zu bewältigen waren, suchte ZKW nach einer besseren Lösung – und wurde bei EPLAN fündig. Die Engineering-Experten aus Wieselburg arbeiten nun seit einiger Zeit mit EPLAN Pro Panel, natürlich inklusive EPLAN Electric P8, und verfügen damit über eine stabile Basis für die Planung des gesamten elektrischen Teils der Montagelinien in 2D bzw. 3D. Optimal ergänzt wird dieser Ansatz durch die cloudbasierte Automatisierungslösung EPLAN eBUILD, die die Planung und Dokumentation maßgeblich unterstützt. „Wir setzen stark auf größtmögliche Standardisierung und Modularisierung unserer Montagelinien, nicht zuletzt, um die Time-to-Market so kurz wie möglich zu halten“, erläutert Alexander Klemenz. Dies spiegelt sich im Engineering und „beginnt bei der schnelleren Produktauswahl, geht über die beschleunigte Konstruktion und bis hin zur zeitoptimierten Umsetzung.“ Die Verwendung von EPLAN kommt ZKW also voll und ganz entgegen: Mit kaum einer anderen Lösung wäre es so einfach und effizient, zukünftige Änderungen an einer Montagelinie von Anfang an mit zu berücksichtigen und, wenn es so weit ist, diese problemlos und zeitoptimiert umzusetzen. „Und dank eBuild profitieren wir zudem von der automatisierten Erstellung der Schaltpläne, die immer auf den selben Standards basieren“, ergänzen Johannes Lagler und Reinhard Wurzer, Process Engineering Operation Resources/Control Engineering bei ZKW. „So ist eine enorme Zeitersparnis beim Engineering realisierbar“, sind sich alle drei Anwender einig. Mit der Einführung von EPLAN einher ging übrigens eine maßgebliche Anpassung der internen Strukturen der ZKW-Engineering-Abteilung, die sich sehr vorteilhaft auf die Transparenz der Abläufe ausgewirkt hat. Nicht unerwähnt lassen möchte Alexander Klemenz schließlich das EPLAN Data Portal: „Mit diesem haben wir direkten Online-Zugriff auf hochwertige Produktkataloge aus einer großen Anzahl namhafter Komponentenhersteller. Wir können stets auf die erforderlichen Daten zurückgreifen die Komponenten ohne Umwege in den Engineering-Prozess übernehmen. Das ist für uns ein mittlerweile unerlässliches Feature, welches uns EPLAN bietet.“
Umsteigen, trainieren, profitieren
Von einer Softwarelösung auf eine völlig neue umzusteigen sehen viele Unternehmen durchaus als Hürde bzw. begegnen dem zumindest mit Respekt. Doch das ist oft unbegründet, wie sich im konkreten Fall zeigt. Johannes Lagler fallen dazu zuerst zwei Worte ein: „einfach und unkompliziert“. Und das, obwohl die ersten Schritte mit EPLAN ins Jahr 2020 fielen, also den Beginn der Corona-Pandemie. Es wurde gemeinsam ein Konzept mit einem konkreten Ziel definiert und dieses dann Schritt für Schritt umgesetzt. „Kompetente EPLAN-Mitarbeiter, spezifisch auf uns vorbereitet und auch auf die erschwerten Bedingungen eingestellt, machten uns den Start tatsächlich sehr einfach und gestalteten den Umstieg reibungslos.“ Individuell abgestimmte Schulungen und Trainings – zuerst pandemiebedingt online, später in Präsenz vor Ort bei ZKW – ergänzten das Angebot optimal. „Bei EPLAN haben wir immer denselben Ansprechpartner, der mit uns und unseren Anliegen vertraut ist. Das schätzen wir besonders“, betont Johannes Lagler.
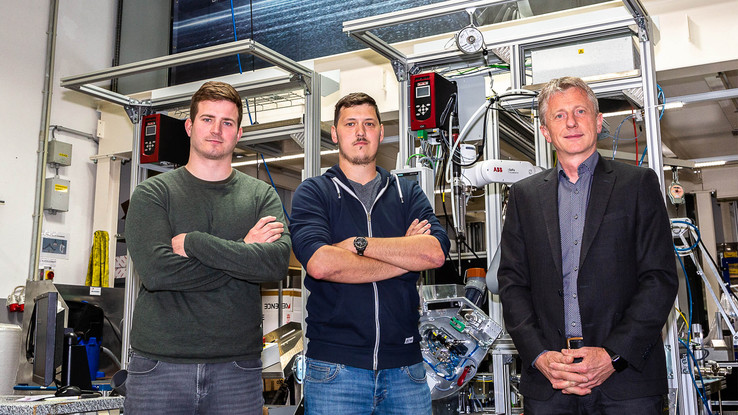
„Mit EPLAN sind wir flexibler und schneller.“ V. li.: Alexander Klemenz, Johannes Lagler (beide ZKW) und Erwin Kreuzer (EPLAN).
© www.martingold.at
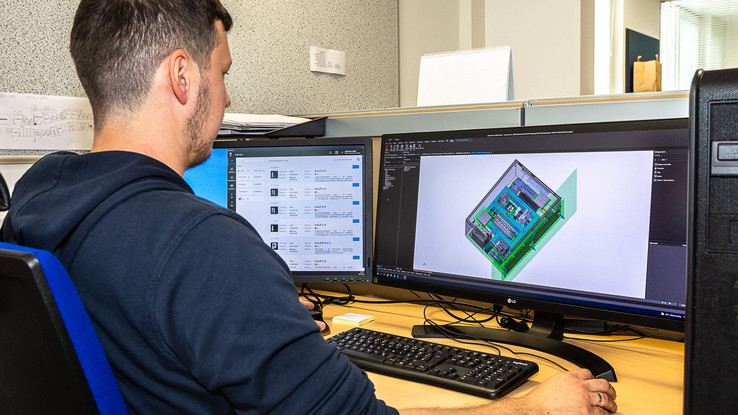
Die Einführung der EPLAN Softwarelösungen bei ZKW verlief dank optimaler Unterstützung reibungslos und unkompliziert.
© www.martingold.at
Autor: Ing. Martin Gold, Journalist, Autor und Fotograf, Wien