Kosteneffizienter Schaltschrankbau
Ein Mann, ein Schaltschrank, eine Woche. Ist diese Formel noch aktuell? Und gibt es Wege heraus aus diesem Kosten- und Ressourcendilemma?
Der Schaltschrankbau in der Schweiz steht unter enormem Druck: hohe Lohnkosten, fehlende Fachkräfte und Verlagerung der Produktion ins Ausland. Dazu kommen teure, zeitfressende Änderungen in letzter Minute und heterogene, nicht aufeinander abgestimmte Prozesse von der Auslegung bis zum Betrieb.
Die Studie Schaltschrankbau 4.0 von EPLAN in Zusammenarbeit mit dem Institut für Steuerungstechnik der Werkzeugmaschinen und Fertigungseinrichtungen der Universität Stuttgart untersuchte die Effizienz von Engineering und Fertigung im Schaltanlagenbau. Es hat sich gezeigt, dass für beide Bereiche noch erhebliches Verbesserungspotential vorhanden ist. Dieser Artikel zeigt die wichtigsten Erkenntnisse auf.
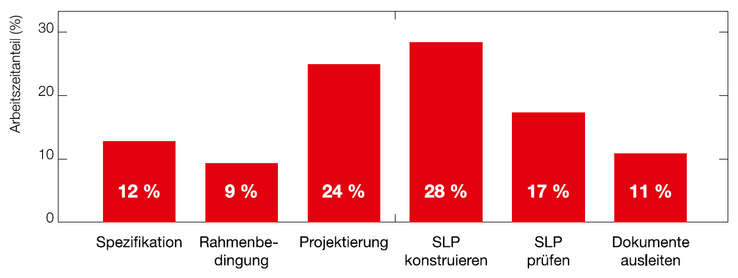
Engineering
Die obenstehende Grafik zeigt die Anteile typischer Arbeitsschritte im Engineering an der gesamten Konstruktionszeit eines Schaltschranks. Für deren Realisierung wird grob zwischen drei Methoden unterschieden:
1. Klassisch – das bedeutet Projekt- oder auftragsorientiertes Arbeiten, Erstellung des Stromlaufplanes (SLP), schematischer Aufbauplan und Stückliste in Excel (manuell).
2. Standardisiert – vorlagenorientiertes Engineering unter Verwendung von Templates, automatische Drahtzuglisten erzeugbar und hoher Wiederholungsgrad.
3. Automatisiert – unter Einsatz von Generierungs- und Optionentechnik, je nach dem auch mittels Maximalprojekt sowie Hersteller-Konfiguratoren.
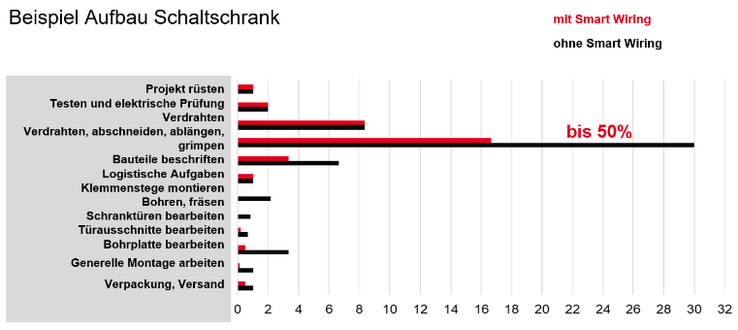
Fertigung
Die obenstehende Grafik zeigt die Anteile typischer Arbeitsschritte bei der Fertigung eines Schaltschranks. Wie beim Engineering kann auch hier die Fertigungsmethode ähnlich beurteilt werden:
1. Klassisch – Basis der Fertigung ist der Stromlaufplan, Seite für Seite wird gefertigt. Keine Konfektionierung möglich.
2. Standardisiert – als Basis dienen hier Listen. Konfektionierung ist möglich, NC Maschinen werden unterstützt, Drahtsätze können gefertigt werden. Teilweise Fliessfertigung.
3. Automatisiert – Linienfertigung und Handlingsysteme werden unterstützt. Konfektionierung aller Komponenten wird erreicht. Die Auslastung von Maschinen kann optimiert werden.
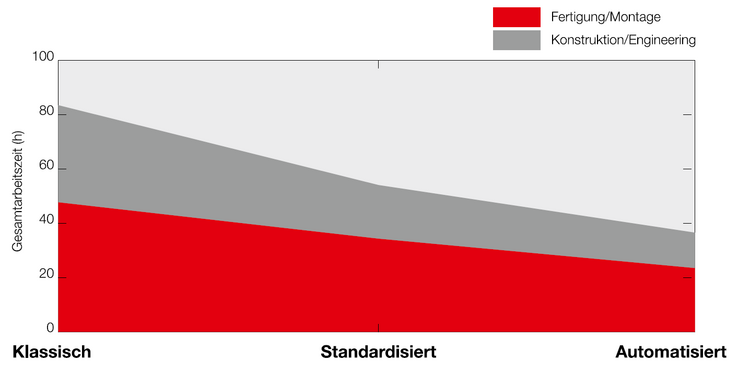
Fertigung
Allein durch die Einführung eines standardisierten Engineerings lassen sich in diesem Bereich bereits 45% Effizienzsteigerung realisieren. Bei der Fertigung besteht der grösste Aufwand in der Verdrahtung. Alleine dieser Arbeitsschritt kann bis 50% effizienter durchgeführt werden. Über alles gesehen lassen sich die in der Grafik aufgeführten Potentiale ausschöpfen. Bis über 60% Einsparungen sind möglich.
Wenn Sie mehr über den modernen Schaltschrankbau erfahren wollen, dann laden Sie das Whitepaper «Elektrisiert – Der digitale Zwilling» herunter.